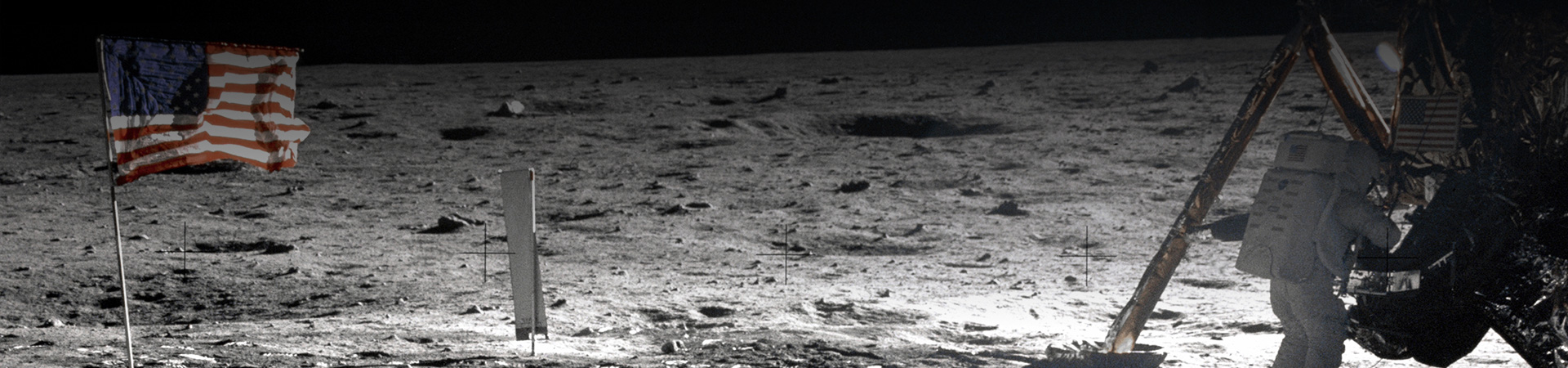
Electrically Initiated, One-shot Release Mechanism
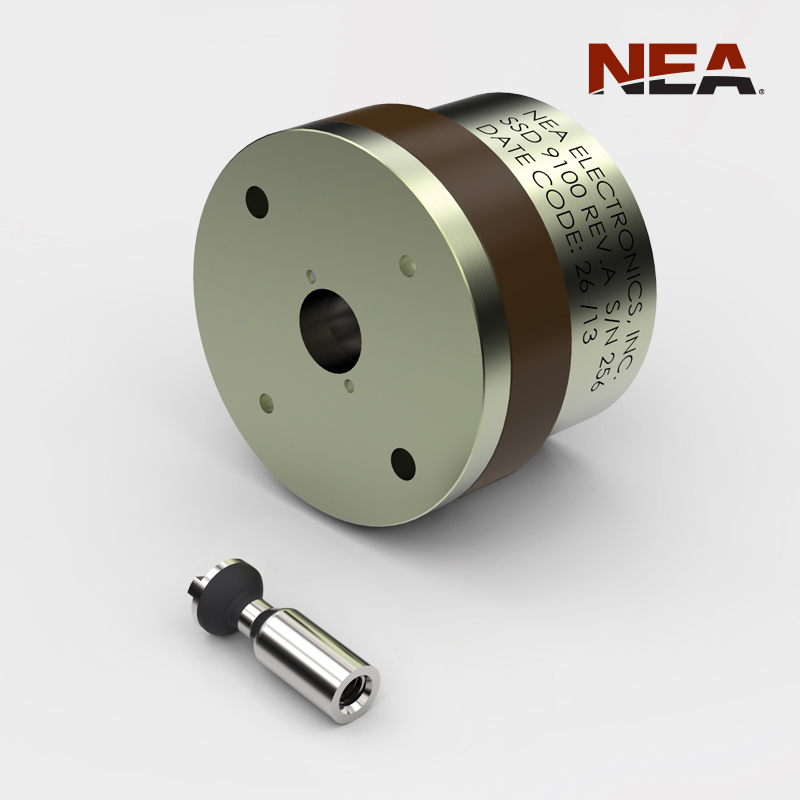
Overview
EBAD is the global leader in non-pyrotechnic Hold Down & Release Mechanisms (HDRM) for the spacecraft market. Hold Down & Release Mechanisms, also sometimes referred to as Separation Nut Release Mechanisms, are offered in a range of sizes with load capacities up to a 500 kN (112,000 pounds force).
Principle of Operation
The EBAD NEA® HDRM is an electrically initiated, one-shot release mechanism that has the ability to carry a very high tensile preload until commanded to release. The preload is applied through a release rod held in place by two separable spool halves which are in turn held together by tight winding of restraining wire. The restraint wire is held in place by redundant electrical fuse wires; actuation of either circuit allows release, assuring maximum reliability. When sufficient electrical current is applied, the restraint wire unwinds allowing the spool halves to separate releasing the release rod and the associated preload.
The actuation is simple and reliable and forms the basis of actuation for many of EBAD’s other products including Pin Pullers, Battery Cell Bypass Switches, and Non-Pyrotechnic Valves.
EBAD has the capability to pair our HDRMs with other hardware such as custom release rods, preload nuts, extractors, bolt catchers, mounting brackets, springs, connectors and electrical harnessing to provide low-shock, high reliability release assemblies.
Applications
Typical applications include:
- Antennas
- Scientific instruments
- Solar arrays
- Reflectors
- Satellite, spacecraft payloads
- Booms and masts
- Stage separation
- Caging mechanisms
Key Features
- Extremely low release shock
- Redundant or non-redundant actuation circuit
- Near simultaneous release of multiple hold-down points (<10 ms)
- Internal torque containment
- Allows up to 6° of angular misalignment
- Extended operating temperature range
- Can be operated with pyrotechnic initiation circuitry
- Range safety friendly
- Space-rated materials
- Factory refurbishment
EBAD release device technology provides significant advantages.
Low Shock — There are three sources of shock with traditional pyrotechnic release devices; those include the pyrotechnic initiator and the resulting transfer of kinetic energy within the mechanism. The EBAD approach eliminates both of these sources of shock. There is no pyrotechnic initiator required so there is no initial shock and the restraint wire release mechanism is also not a significant contributor to shock.
A third source of shock is the energy stored in the release rod itself as well as any of the other components that are in the preload path. The nature of EBAD device’s gentle release of preload allows this stored energy to be dissipated over the release event minimizing the stored energy contribution to shock as well.
Fast Acting — With respect to shock, the action of EBAD devices is quite gentle yet the release event itself is still very fast. Since the fuse wire is extremely small the release event can be triggered in milliseconds. This capability allows multiple EBAD devices to be used in parallel where simultaneous release is required, such as large solar array panels and spacecraft stage separations.
Reliable —With simplicity comes reliability. The basic design of the EBAD NEA® HDRM is very simple with a minimum of moving components. The devices are robust and not sensitive to extreme environments or contaminants. High reliability is supported both analytically and by an extensive history of successful operation in mission critical applications.
Light Weight — EBAD devices offer extremely high preload release capacities versus unit mass. Some EBAD NEA® HDRM models have specific preload release capacities greater than 300N/g.
Temperature Insensitive — The simplicity of the EBAD release device mechanism is an asset not just for reliability but also with respect to temperature sensitivity. EBAD NEA® HDRMs are insensitive to extreme temperatures. Specific EBAD NEA® HDRMs have been qualified for operation at temperatures as low as 25K. The extreme low mass of the fuse wire results in actuation performance that insensitive to initial conditions.
Low Risk — EBAD NEA® HDRMs have an extensive history of use on a broad variety of spaceflight applications and are currently the baseline release device of choice on most major spacecraft buses. This history of reliability and mission success makes the NEA® HDRM our customers’ low risk option.
Compatible — EBAD NEA® HDRM devices have been designed to work with existing pyro firing circuits. The flexibility of the design however also allows operation with lower firing current if required.
Key features of EBAD’s non-pyro NEA® Hold Down Release Mechanism (HDRM) include having extremely low release shock, near simultaneous release of multiple hold-down points, redundant actuation circuits with low current needs, and the widest operating temperature range. With minimal moving components, the NEA® HDRM’s relatively simple split spool design allows for high reliability. These crucial products for the space and satellite industries also work within extended operating temperature ranges and, if needed, could be operated with pyrotechnical initiation circuitry.
Contact us for more information on this product
Custom Configurations
In addition to our line of standard HDRM devices EBAD can provide custom configurations that include; modifications to the mechanical interface, modified housing designs, changes to lead wires, revisions to load capability, additional connector housings, and release rod capture assemblies. EBAD can also provide HDRM devices as part of a next higher assembly either built to our customer’s prints or designed at EBAD to our customer’s specifications.
Many of our current customers rely on EBAD’s in-house engineering expertise to integrate our market leading split-spool HDRM technology into custom assemblies to improve their competitive edge.
For more information:
*Commercial Item per FAR 2.101
Typical HDRM Actuation Curve
A typical HDRM actuation curve showing the actuation time as a function of the actuation current is presented below. Please contact our applications engineers for specific curves for each product.
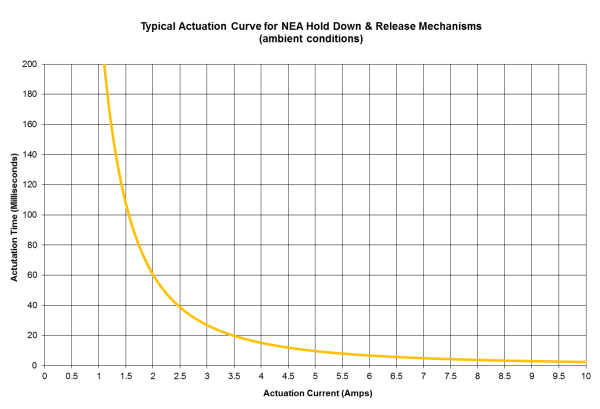
Model | Size | Release Load | Proof Load | Dimensions ( Dia x Height) | Mass | Data Sheet | CAD |
---|---|---|---|---|---|---|---|
9040 | #4 (112-40) | 1.1kN (250 lb f) | 1.3kN (300 lb f) | 15.7mm (0.618″) x 20.6mm (0.811″) x 21.7mmH (0.855″) (with release rod 40.8mm / 1.605″) | 13.6g (.03 lb) | Download PDF | Contact Us |
9100 | M3 (1/8”) | 6kN (1,360 lb f) | 7.6kN (1,700lb f) | Ø31.8mm x 28mm (Ø1.25” x 1.10”) | 70 g (0.15 lb | Download PDF | Contact Us |
9102 | M6 (1/4”) | 17.8kN (4,000lb f) | 22.2kN (5,000lb f) | Ø43.2mm x 39.4mm (Ø1.70” x 1.55”) | 130 g (0.29 lb | Download PDF | Contact Us |
9103 | M10 (3/8”) | 35.0kN (7,868lb f) | 41.0kN (9.217lb f) | Ø48.3mm x 40.6mm (Ø1.90” x 1.60”) | 200g (0.44 lbm) | Download PDF | Contact Us |
9104 | M12 (1/2”) | 67kN (15,000 lb f) | 84kN (18,750 lbf) | Ø63.2mm x 46.9mm (Ø2.50” x 1.845”) | 300g (0.66 lbm) | Download PDF | Contact Us |
9106 | M16 (5/8”) | 142kN (32,000lb f) | 178kN (40,000lb f) | Ø69.9mm x 54.4mm (Ø2.75” x 2.14”) | 700 g (1.5 lb | Download PDF | Contact Us |
9107 | M19 (3/4”) | 205kN (46,000 lb f) | 260kN (58,500 lb f) | Ø99.3mm x 82.8mm (Ø3.91” x 3.26”) | 2526 g (5.57 lb | Download PDF | Contact Us |
9108 | M25 (1”) | 320 kN (72,000 lb f) | 384 kN (86,400 lb f) | Ø117.6mm x 111mm (Ø5.13” x 4.9”) | 3855 g (8.5 lb | Download PDF | Contact Us |
EBAD has qualified cup/cone and low shock bolt retraction interfaces for our NEA® HDRM devices. These devices are able to handle high shear forces and are designed to handle applications such as satellite deployments and payload releases. Other configurations are available, please contact EBAD for more information.